Werkstoffe
Wir produzieren für Sie metallische Verbindungselemente aus folgenden Werkstoffen:
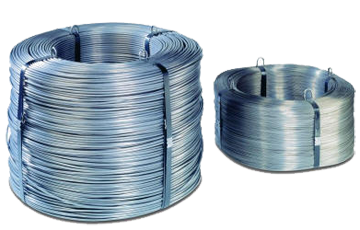
niedriglegierte Stähle | nach DIN EN 10263-2 (für Verbindungselemente ohne Wärmebehandlung, z.B. C10C) |
Einsatzstähle | z.B. SAE 1018, SAE 1022 |
Vergütungsstähle | z.B. SAE 1022, 23MnB4, vergütet auf z.B. Rm min. 1040 N/mm² Standard für EJOT PT®, DELTA PT®, Duro-PT®, ALtracs® Plus |
austenitischer Edelstahl A2 1.4303 | X4CrNi 18-12 (bevorzugtes Material für gewindefurchende Schrauben Ø >= 3,0 mm) |
austenitischer Edelstahl A2 1.4301 | X5CrNi 18-8 |
austenitischer Edelstahl A2 1.4567 | X3CrNiCu 18-9-4 (bevorzugtes Material für Kleinstschrauben Ø <= 2,5 mm) |
austenitischer Edelstahl A4 1.4401 | X5CrNiMo 17-12-2 (auf Anfrage) |
ferritischer Edelstahl F1 1.4016 | X6Cr17 ferritischer Chromstahl |
Aluminium Werkstoffe | (auf Anfrage) |
Bitte beachten Sie bei der Bestellung von Schrauben aus Edelstahl:
Der Begriff "Edelstahl rostfrei" bezeichnet eine Gruppe von Stählen, welche an ihrer Oberfläche eine Chromreiche Oxidschicht aufweist. Dazu zählt unter anderem die Gruppe der austenitischen Edelstähle (Edelstahl A2 und A4).
Diese Oxidschicht wird auch als Passivierungsschicht bezeichnet und ist für den Korrosionsschutz verantwortlich. Auch im Fall von Beschädigungen bildet sich diese Passivschicht unter dem Einfluss von Sauerstoff immer wieder neu.
Die Bildung der Passivschicht kann auch durch ein zusätzliches chemisches Passivieren (z.B. nach ISO 16048) beschleunigt werden. Dieses Passivieren ist nicht mit einer künstlich erzeugten Passivierung auf Zink zu vergleichen. Soweit nichts anderes vereinbart wurde, müssen Verbindungselemente gemäß der DIN EN ISO 3506-4 sauber und metallisch blank geliefert werden. Um eine größtmögliche Korrosionsbeständigkeit zu erreichen, wird eine Passivierung empfohlen. Wird eine Passivierung gefordert, so ist diese nach ISO 16048 durchzuführen.
Die Korrosionsbeständigkeit von austenitischen Edelstählen läßt sich nicht mit einem Salzsprühnebeltest bestimmen. Der Salzsprühnebeltest wurde als Prüfverfahren zum Aufzeigen von Schwachstellen in Schichtsystemen (z.B. galvanische Schichtsysteme oder organisch/anorganische Schichtsysteme) vorgesehen.
Verbindungselemente aus austenitischem Edelstahl, welche einem Salzsprühnebeltest unterzogen werden, werden definitiv rosten. Der Grund liegt darin, dass die Oxidschicht durch den Salzsprühnebel zerstört wird und sich durch die dauerhafte Besprühung keine neue Oxidschicht bilden kann. Aus diesem Grund kann der Korrosionsschutz von Edelstahlschrauben auch nicht durch einen Salzsprühnebeltest mit galvanisch bzw. anorganisch/organisch beschichteten Schrauben verglichen werden.
Uns sind auch keine Normen bekannt, worin Verbindungselemente aus Edelstahl einem Salzsprühnebeltest unterzogen werden. Unter der Voraussetzung, dass ein Verbindungselement aus austenitischem Edelstahl mit Sauerstoff in Berührung kommt und somit eine entsprechende Oxidschicht aufweist, wird ein solches Bauteil einem herkömmlichen Verbindungselement aus niedriglegiertem Stahl (welches dann natürlich eine galvanische oder anorganisch/organische Oberfläche aufweist) vom Korrosionsschutz überlegen sein.